Phone Case for Cellairis
Industrial Design
.webp)
THE BRIEF
Revolutionising Protective Phone Cases: Defying Manufacturing Convention by Design Innovation
Step into the future of phone protection with Cellairis' Showcase rugged iPhone cases, a groundbreaking project aimed at redefining the traditional concept of protective phone cases. This project was born out of a mission to challenge the status quo of protective case manufacturing.
By ingeniously combining soft and hard materials without the need for co-molding, we aimed to create a phone case that not only offers unparalleled protection but also maintains a sleek and lightweight design. Our vision was to revolutionise the protective phone case market, providing users with a product that not only safeguards their devices but also enhances their overall user experience.In a world where protective phone cases have become synonymous with bulkiness and rigidity, the Cellairis Showcase sought to defy convention. We recognized the need for a paradigm shift in protective case design, one that prioritises both protection and user experience. With this in mind, we embarked on a journey of innovation and creativity, determined to develop a product that challenges industry norms and sets new standards for excellence.
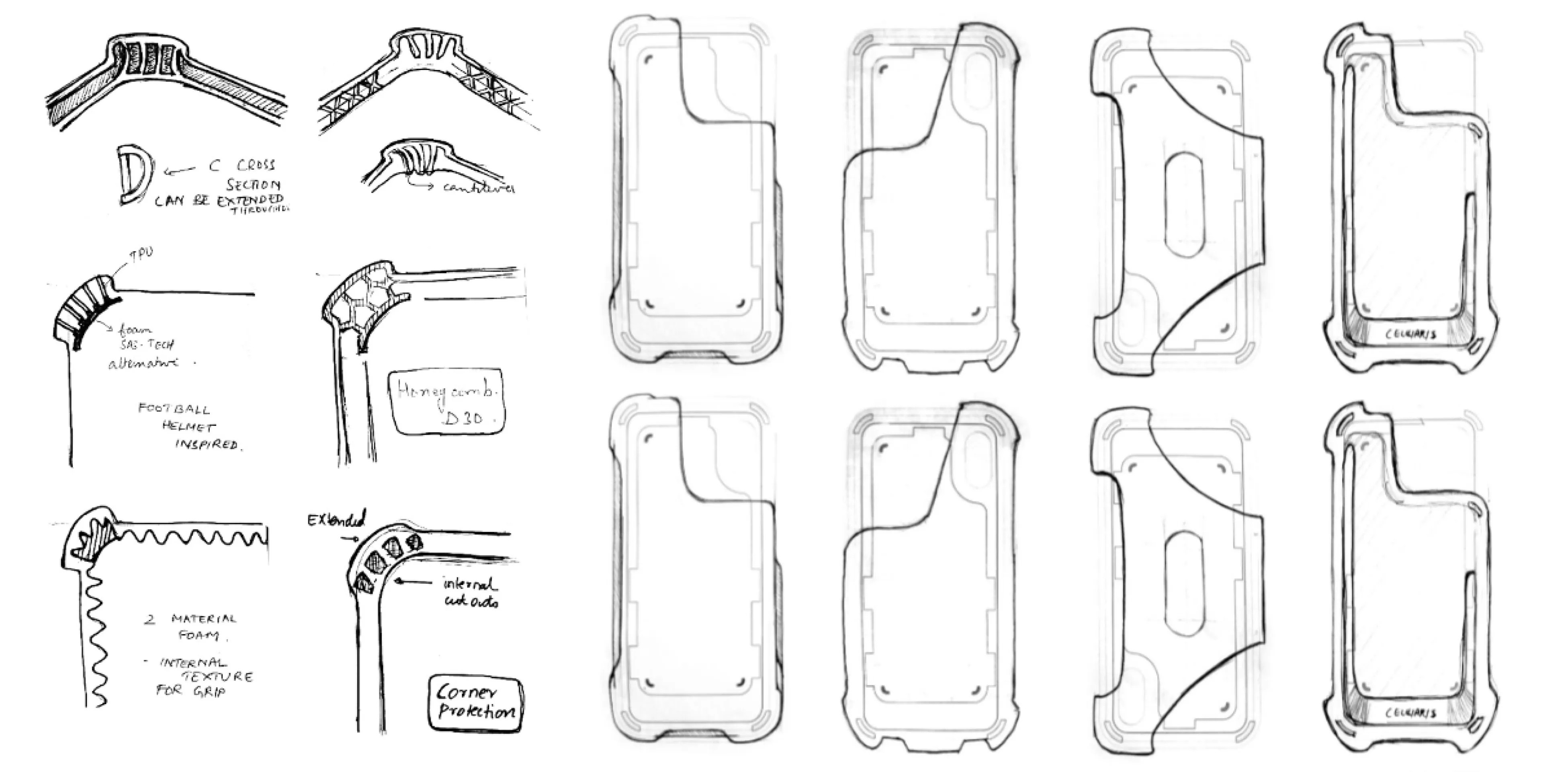
ideation
Innovating the Future of Phone Protection
The journey of conceptualising the Cellairis Showcase phone cases began with a meticulous exploration of the challenges plaguing the protective case industry. Traditional manufacturing processes often resulted in bulky and inflexible cases, limiting design innovation and user experience.
Through extensive discussions with stakeholders and thorough market research, we identified key areas for improvement and innovation. Drawing inspiration from diverse industries and regions, we embarked on an ideation process aimed at crafting a truly revolutionary product. Our goal was not only to address existing limitations but also to set new standards in protective case design, offering users a product that seamlessly combines functionality, durability, and aesthetic appeal.Our ideation phase was characterized by a commitment to pushing boundaries and exploring new possibilities. We leveraged insights from various stakeholders, industry experts, and market trends to inform our design decisions. From brainstorming sessions to concept sketches, every step of the process was guided by a relentless pursuit of excellence and innovation. We challenged ourselves to think outside the box, exploring unconventional materials, manufacturing techniques, and design elements to create a product that defies expectations and redefines the protective case landscape.
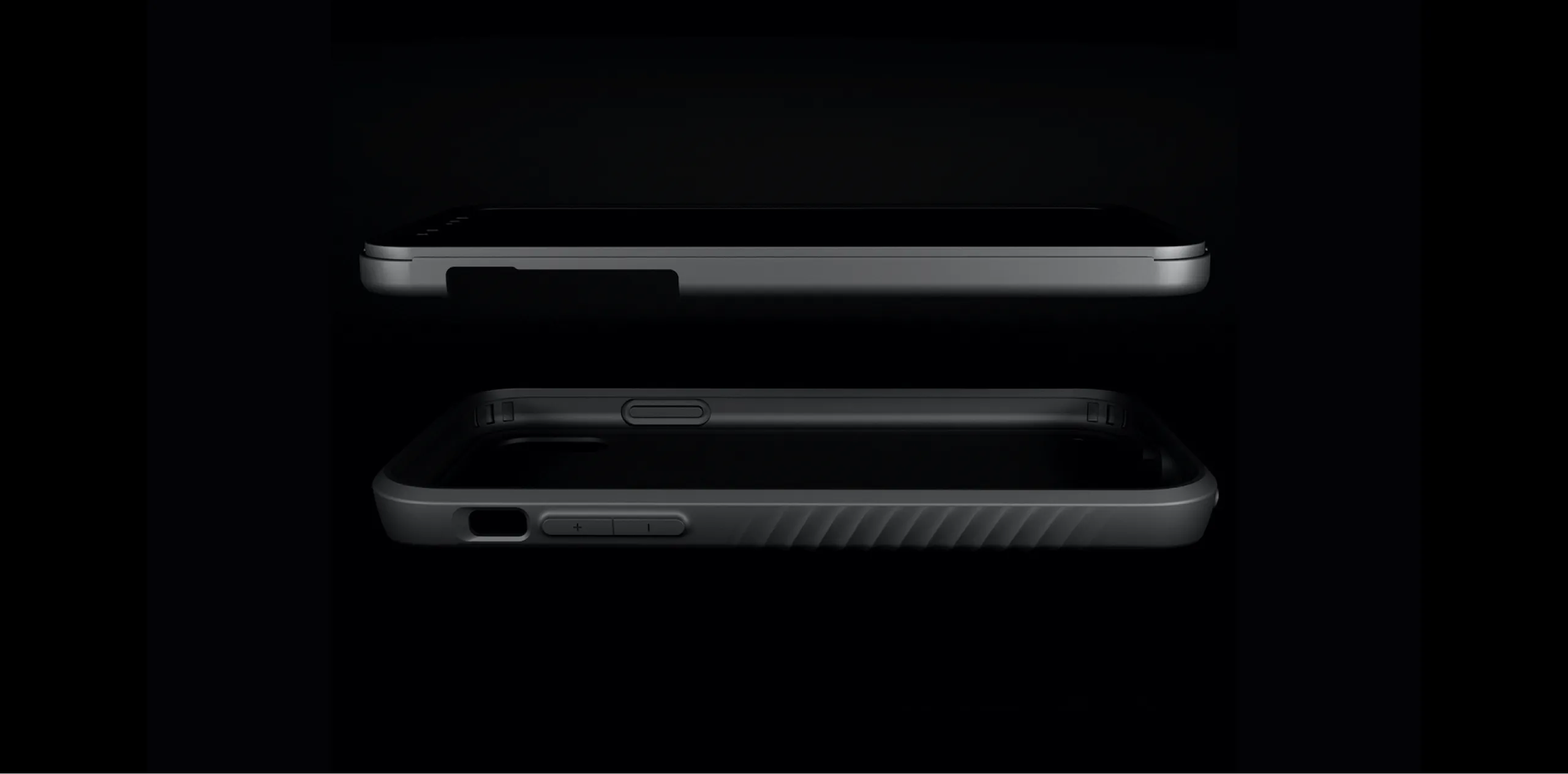
prototyping
Trial, Evolution, and Improvement
The prototyping phase of the Cellairis rugged iPhone case project was marked by a relentless pursuit of perfection. We embarked on an extensive journey of testing, iteration, and refinement to ensure that our product exceeded expectations in every aspect.
From exploring a myriad of materials to experimenting with various manufacturing techniques and design architectures, each prototype underwent rigorous scrutiny. Our primary focus was on optimising durability, functionality, and user experience. We conducted comprehensive tests to ensure compatibility with wireless charging, dust-proofing, and accessibility to ports and buttons. Through continuous iteration based on valuable user feedback and client input, we fine-tuned the design to achieve the perfect balance of protection and aesthetics.Throughout the prototyping process, our commitment to excellence remained unwavering. We pushed the boundaries of traditional protective case design, exploring innovative solutions to address existing challenges. Each iteration brought us closer to our goal of creating a product that not only meets but exceeds the expectations of our users. With meticulous attention to detail and a dedication to innovation, we refined our prototypes to deliver a truly exceptional product that redefines the protective phone case landscape.
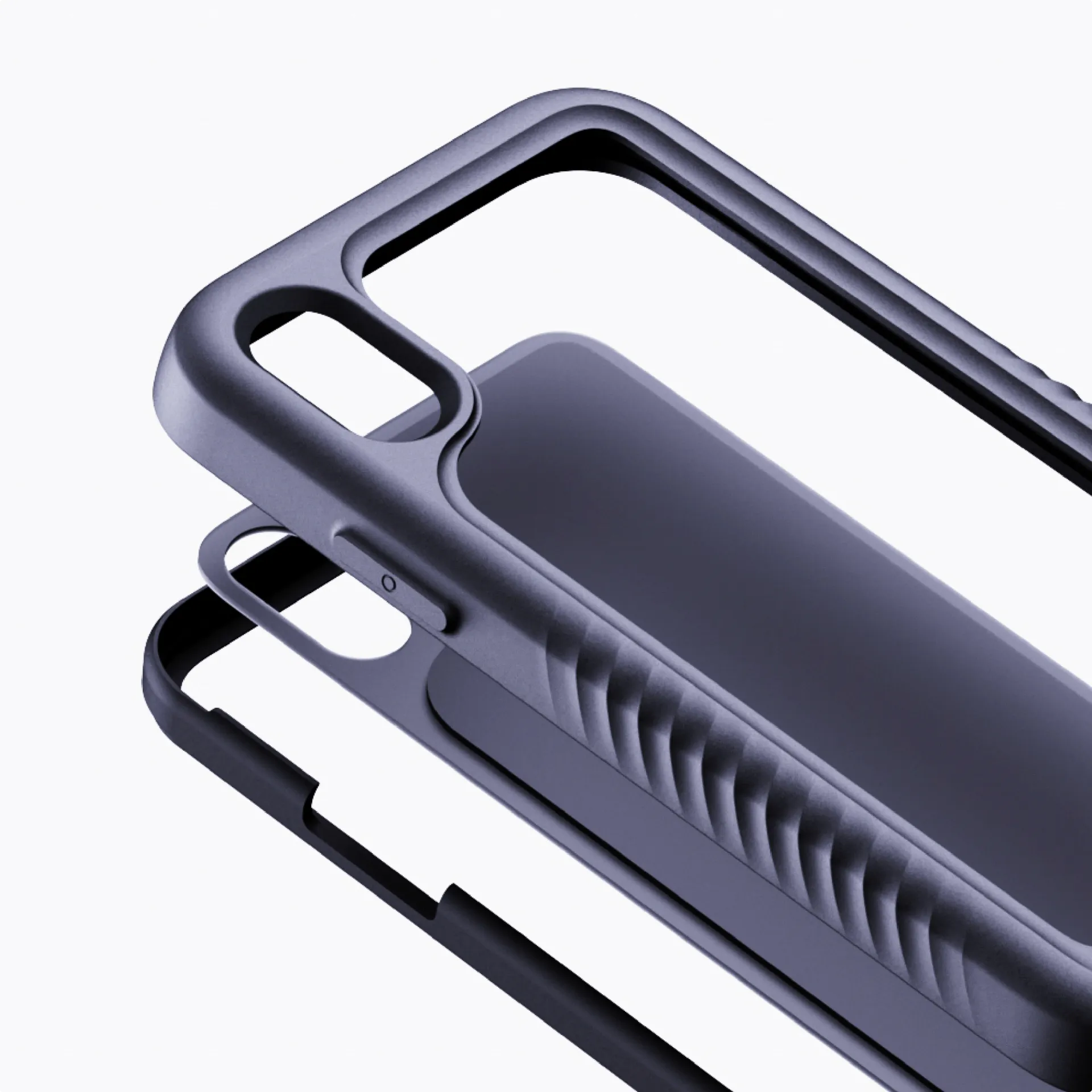
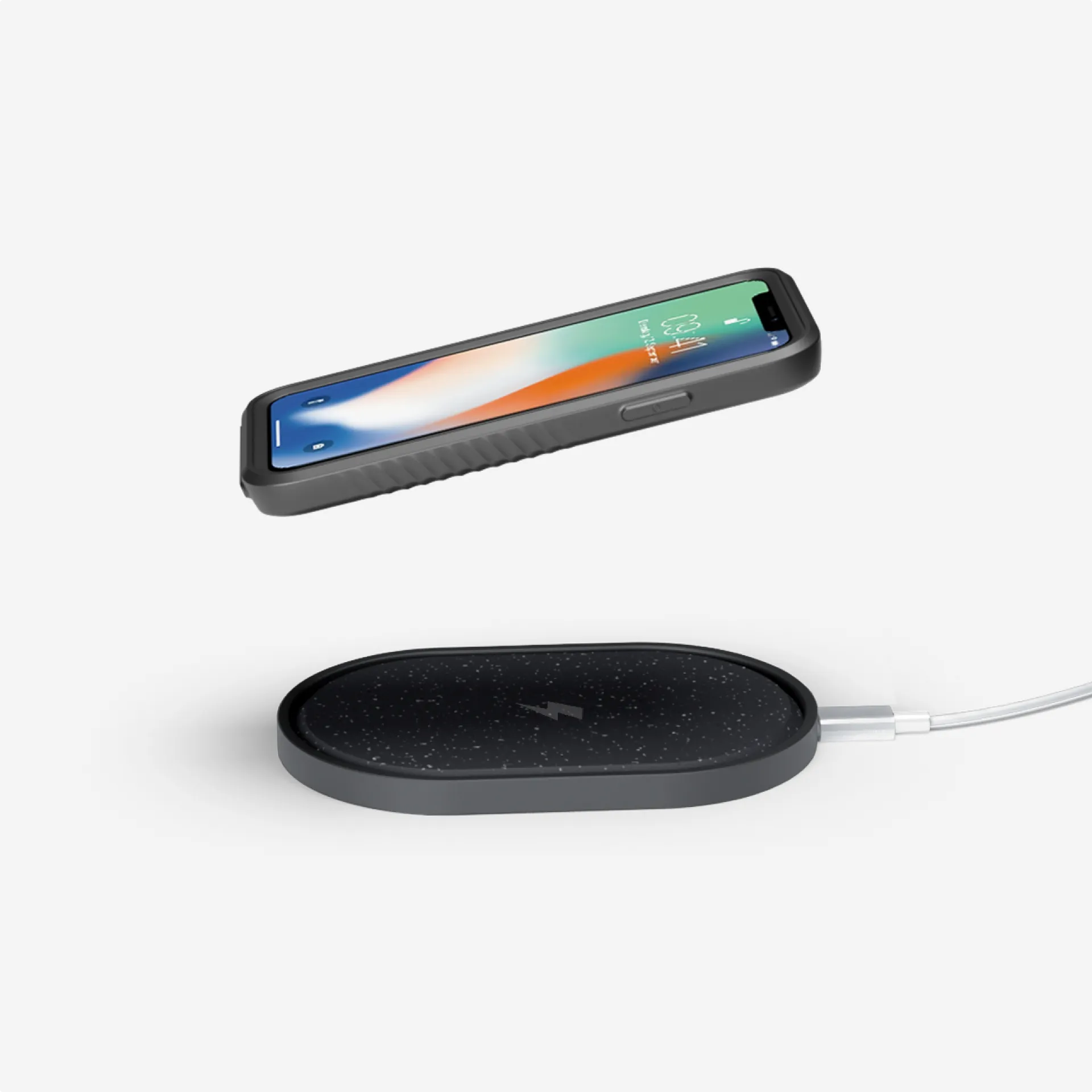
Redefining the Essence of Protection
The Cellairis Showcase iPhone cases are a testament to our commitment to innovation and excellence. Unlike traditional protective cases, our design seamlessly integrates soft and hard materials without the need for co-molding, resulting in a sleek and lightweight yet highly protective case.
What truly sets our product apart is its unique combination of features and functionalities. From the distinctive corner protection mechanism to the ergonomic grip texture and precision-designed openings for cameras, ports, and buttons, every aspect of our design has been meticulously crafted to offer users a superior level of protection and functionality.At Poetic Cases, we believe that innovation is the key to success. Our relentless pursuit of excellence has led us to create a product that challenges industry norms and sets new standards in protective case design. With its unparalleled combination of durability, functionality, and aesthetics, the Cellairis Showcase iPhone cases stand out as a truly one-of-a-kind solution in the market.
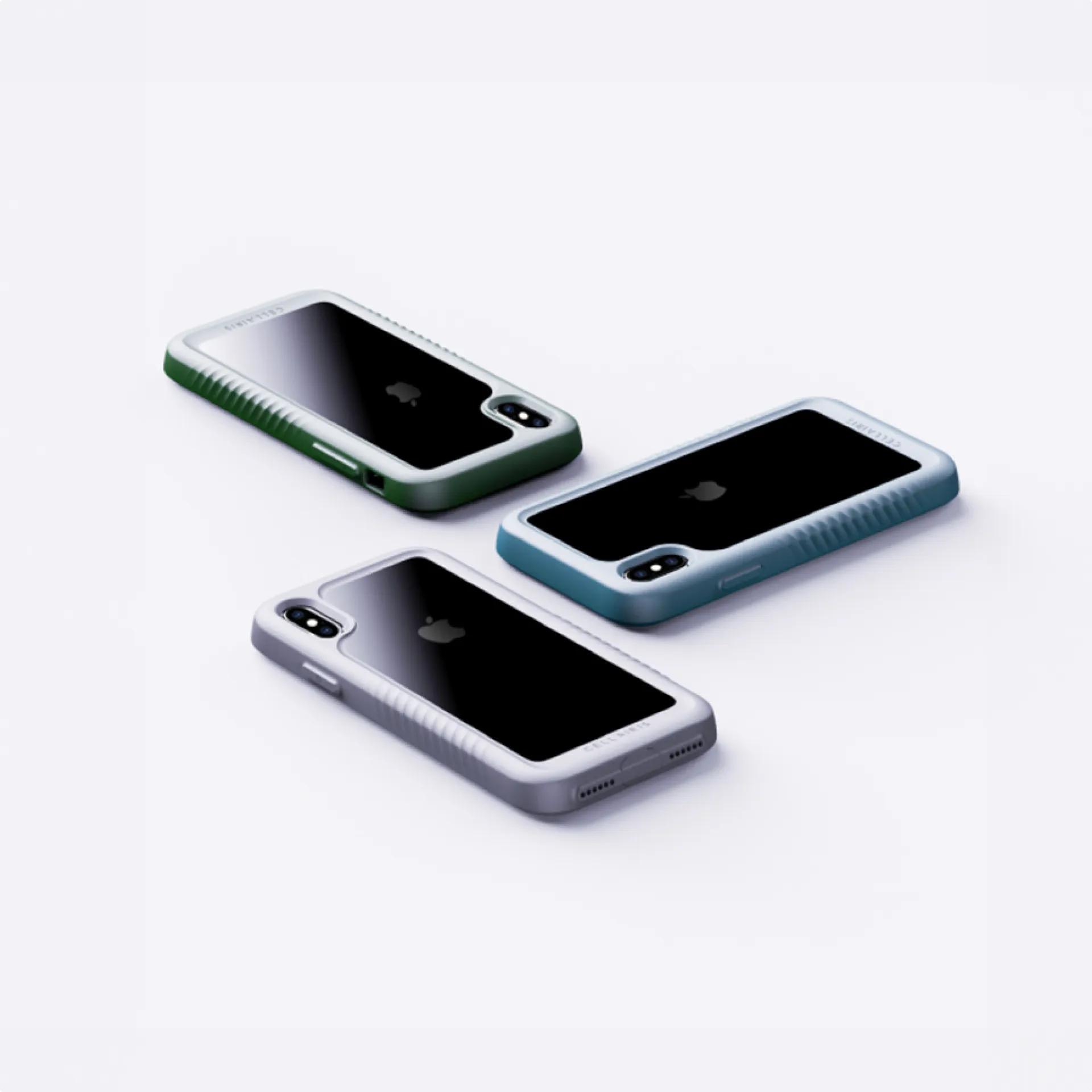
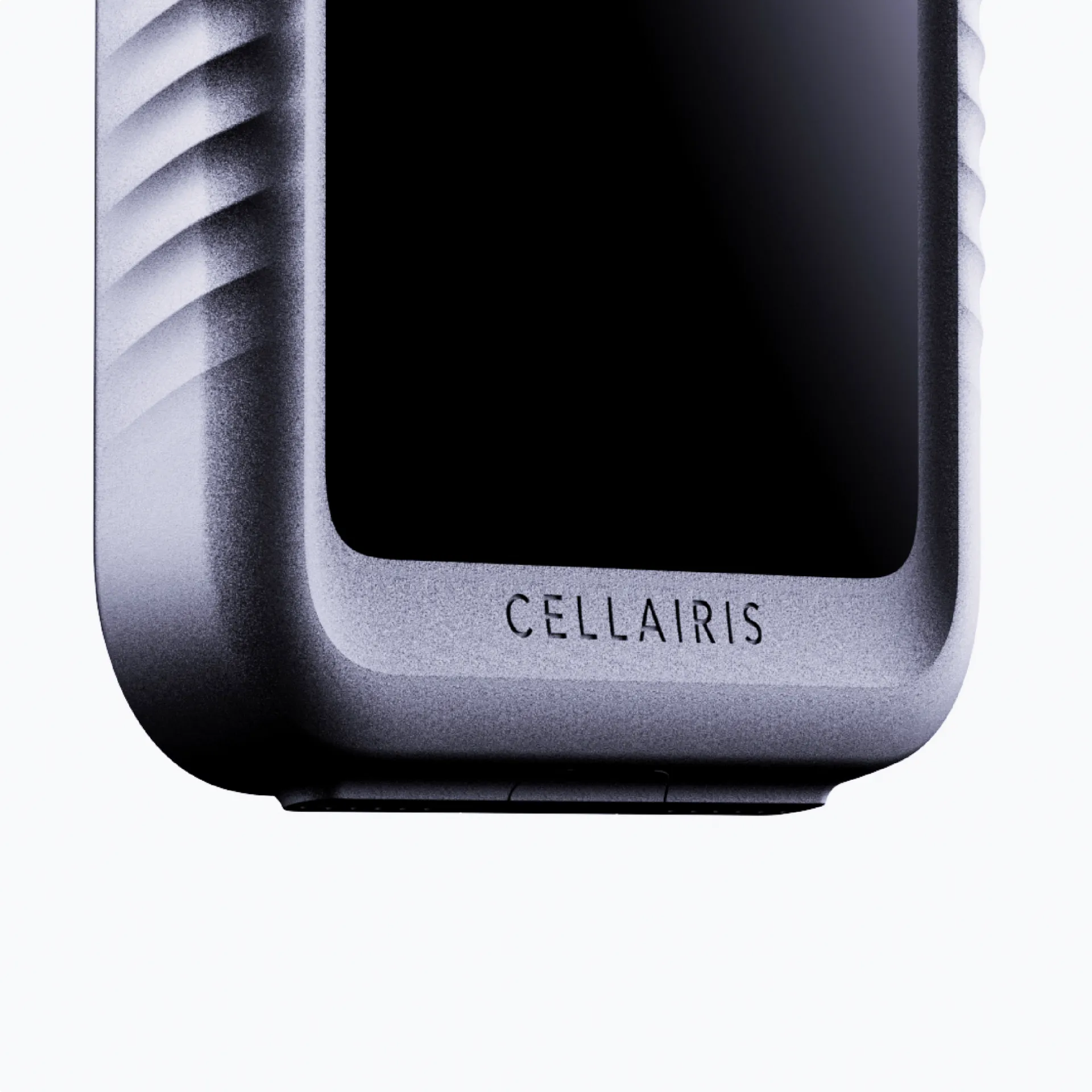
Evolving Phone Cases with Fresh Details
The ergonomic grip texture ensures a secure hold, reducing the risk of accidental slips or drops. Meanwhile, precision-designed openings and tactile buttons offer effortless access to ports and controls, allowing users to navigate their device with ease.
At Analogy, user experience is the cornerstone of our design philosophy. We believe that a truly exceptional product not only offers superior protection but also delivers a seamless and intuitive experience for the user.With this in mind, we engineered the rugged iPhone cases to provide users with unparalleled comfort, convenience, and functionality. Moreover, the lightweight and slim profile of the case enhance overall comfort and usability, ensuring that users can enjoy superior protection without compromising on style or functionality.In our relentless pursuit of excellence, we left no stone unturned in perfecting the user experience of our product. Every aspect of the design, from the texture of the materials to the placement of the buttons, was carefully considered and meticulously optimized to elevate phone protection to new heights. Our goal is not just to meet but to exceed user expectations, providing them with a product that not only safeguards their device but also enhances their overall smartphone experience.
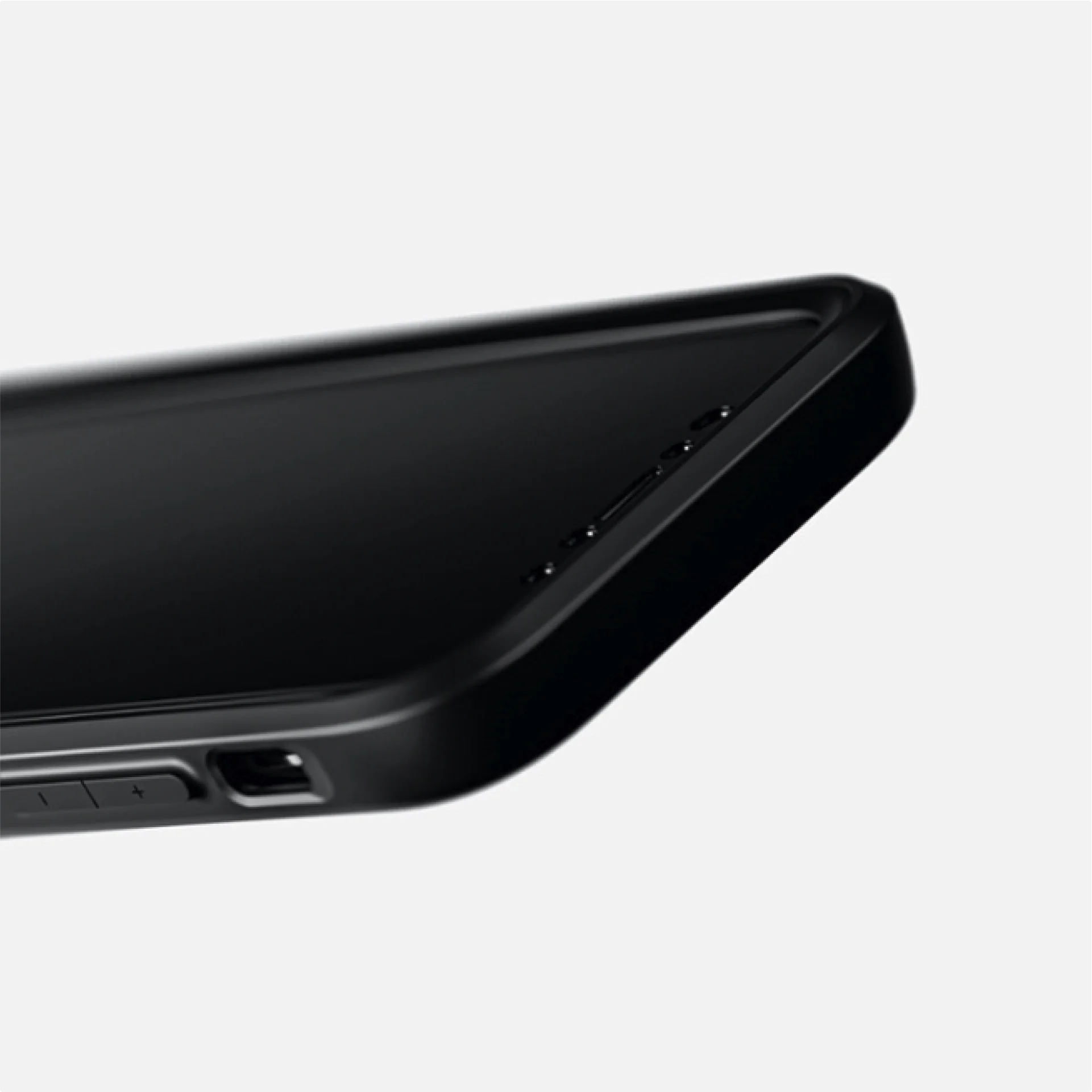
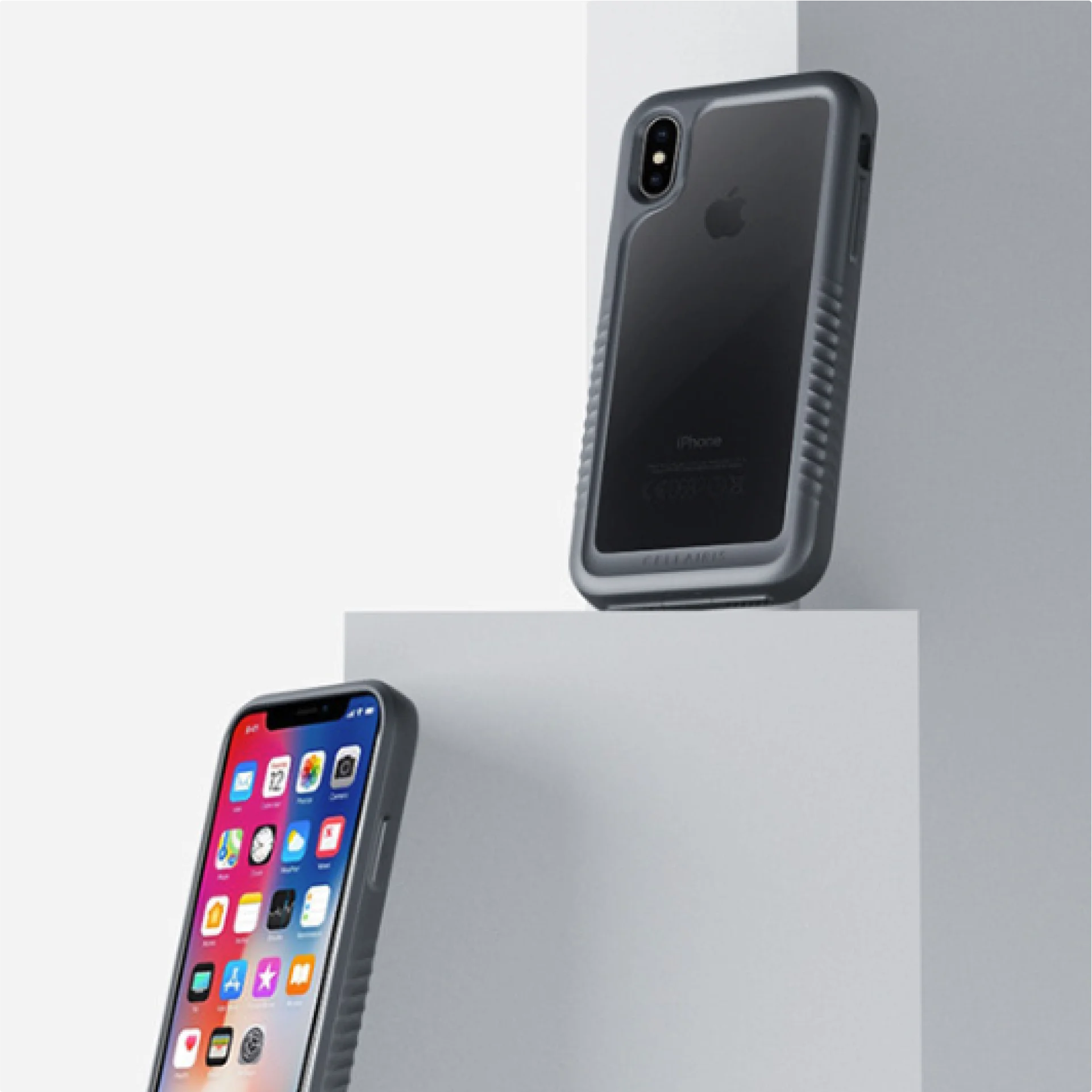
The Science Behind Superior Protection
The integration of soft and hard materials, precision-designed openings, and an ergonomic grip texture ensures maximum protection without compromising on style or functionality. The engineering behind the Cellairis Showcase iPhone cases is a testament to our unwavering commitment to excellence.
We spared no effort in meticulously designing and testing every aspect of the case to optimize its durability, functionality, and user experience.Through a combination of innovative design techniques and rigorous testing protocols, we achieved a perfect balance between protection, aesthetics, and usability. Our dedication to engineering perfection has resulted in a phone case that sets new standards in the industry, redefining what it means to deliver superior protection for smartphones.From the initial concept to the final product, our engineering team worked tirelessly to ensure that every detail was meticulously crafted and rigorously tested. Our goal was not just to create a protective phone case but to engineer a solution that offers users unparalleled peace of mind and satisfaction. With its innovative design, superior materials, and flawless execution, the Cellairis Showcase iPhone cases stand as a testament to our commitment to excellence in engineering.
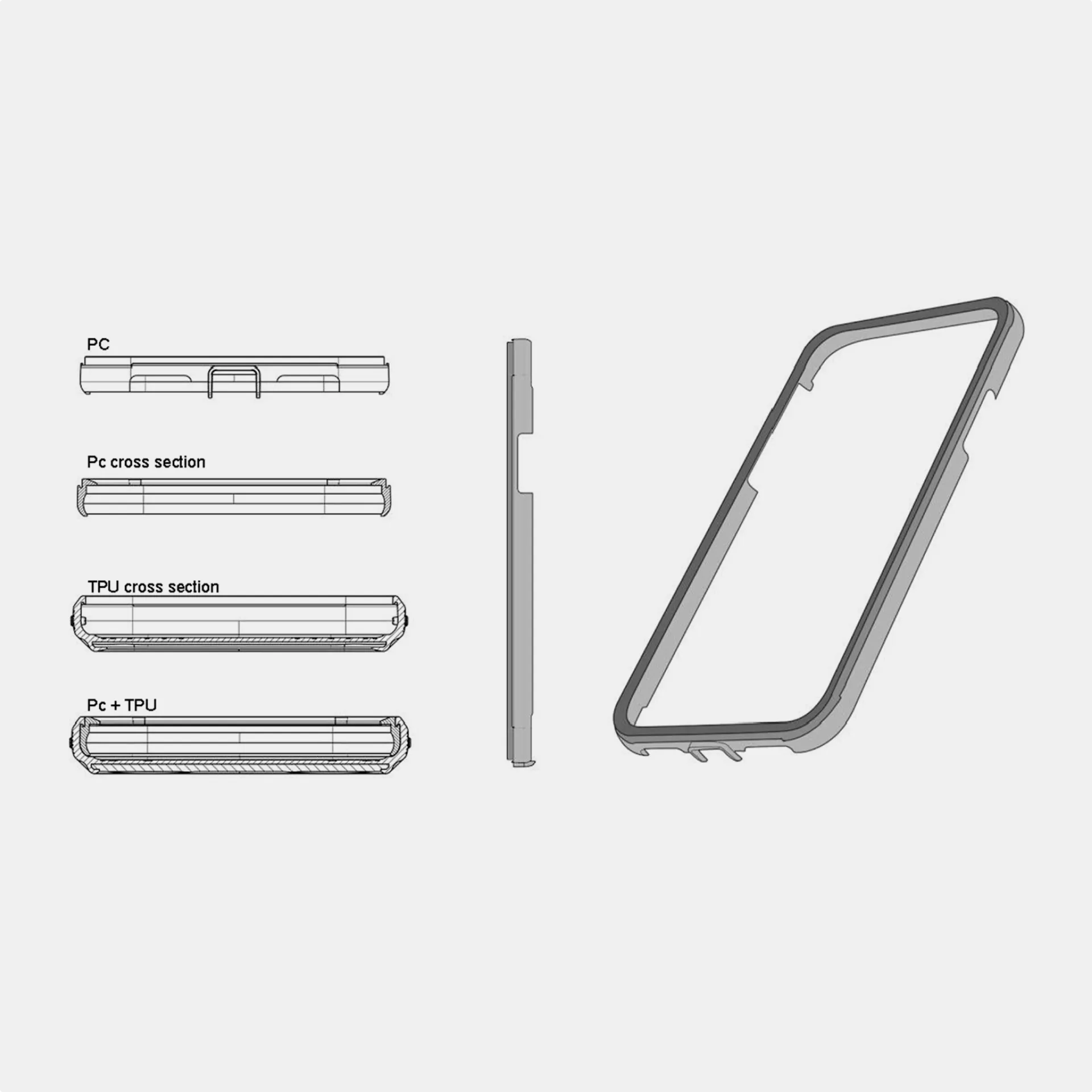
.webp)
The Transformative Impact of Alphacase on Average Tooling Costs
The Cellairis Showcase iPhone case have made a significant impact in the protective phone case market. With a 60% reduction in tooling costs, three times more protection than rival products, and a 25% decrease in bulkiness, our product has redefined the standards of phone protection.
Beyond the numbers, our case has empowered users to enjoy superior protection and functionality, enhancing their overall smartphone experience.Furthermore, our commitment to innovation and excellence extends beyond the product itself. We are actively engaged in initiatives to reduce environmental impact and promote sustainability in the manufacturing process. By embracing new technologies and materials, we aim to lead the industry towards a more sustainable future while continuing to deliver products that exceed customer expectations.
Services
- Industrial design
- Market Research
- Design Language
- Conceptualisation
- Mechanical Engineering
- Product Architecture
- Product Visualisation
- Prototyping
- Production Support
Year
2018-19
Market
USA